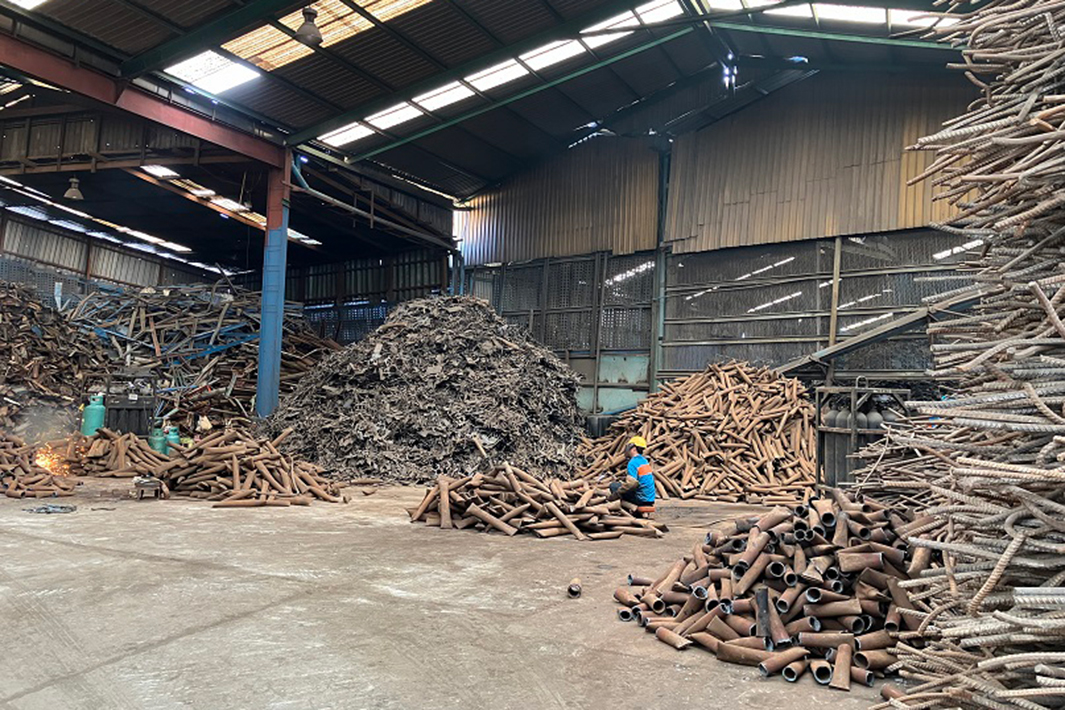
Angprapha Steel (Headquarters: Samut Sakhon Province, President: Angpraphapornchai Chadhin), a local scrap company in Thailand, was established in 2003 and is celebrating its 21st year this year. The company supports local steel production with its strength in handling iron scrap generated at factories. They are also expanding its business by selling stainless steel and non-ferrous scrap as well as used steel materials in addition to iron scrap. I recently toured the company’s headquarters yard.
It takes less than an hour’s drive from Bangkok city. Samut Sakhon province, where the company’s headquarters is located, is an urban area adjacent to Bangkok, facing the sea to the south and famous for its shrimp farming and salt fields. Along the way, construction work to extend subways and roads is being carried out everywhere, and the development of buildings, condominiums, stores, etc. These are giving me impression that Bangkok’s metropolitan atmosphere is gradually spreading to neighboring prefectures.
In addition to the head office yard, the company operates two locations: the Pinthong branch (in Chonburi province) and the largest branch in Krok sombun (in Prachinburi province, 80,000 square meters), with a total handling volume of 10,000 to 20,000 tons per month. The head office yard alone handles 7,000 tons.
The main item is steel scrap, and because each of their bases is adjacent to an industrial park, 90% of the volume handled comes from factories such as home appliance manufacturers and automobile manufacturers. The company places its own collection box at the generation factory, collects them, processes them in-house, and then supplies to domestic induction furnace manufacturers and foundry manufacturers.
The head office yard has a site area of 31,000 square meters, and all storage and work areas are under the roof. Inside the shop, a wide variety of scraps are neatly piled up by type, including new cuttings, heavy metals, foundry and demolition-related scraps, drilled, and tin-plated scraps. As most of the scraps are factory-generated, the scraps themselves are very clean. Nearby, field workers were also working on the pieces by hand using alligator shears.
Workers are Thai and migrant from Laos and Myanmar. Their daily wages are 300 to 400 baht (1,200 to 1,600 yen). To meet customer needs, they cut various type of scraps by using a guillotine shear and alligator shear. I got the impression that there were more workers compared to Japanese scrap companies, probably because there was a lot of manual labor.
Thailand cannot meet domestic demand with domestically generated scrap alone, so it relies on imports for 20% of its total demand. However, in recent years, due to decarbonization and increasing demand for scrap in developing countries. The number of exporters has been increasing. So some steel maker is feeling the necessity of banning exports and restricting export volumes.
Due to the economic downturn, the current generation of scrap is decreasing in almost all fields, and competition with other companies in the same industry to collect scrap is fierce, leading to a strong sense of shortage. “Our challenge is to acquire and expand new purchasing sources. In order to stabilize our management, we would like to actively work on expanding products other than iron.” Angpraphapornchai Chayaporn vice president said.
.